In order for a product to get the NAFICO quality seal, it must successfully go through all the rigorous steps of our quality control process, from the moment it is loaded on the ship to the final delivery to the customer. This quality seal is a formal commitment we make to our customers to ensure that we offer them high-quality animal feed ingredients.
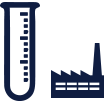
STEP 1
SAMPLING AT THE MANUFACTURING PLANT AND CERTIFICATE OF ANALYSIS PROVIDED BY THE MANUFACTURER
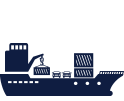
STEP 2
TRANSPORTATION
Products arrive to our warehouses by ship, rail and truck.
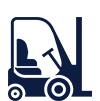
STEP 3
WAREHOUSE ARRIVAL
Upon arrival at the warehouse, the seal and the container are carefully inspected. Lot and container numbers are recorded and confirmed. The products are stacked and stored in a dry, temperature-controlled environment.
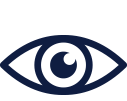
STEP 4
SAMPLING
Samples are taken from every lot number that arrives at our warehouses from overseas. They are then sent to accredited 3rd party laboratories for further analysis.
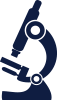
STEP 5
AT THE LABORATORY
The samples are tested for product composition accuracy and for contaminants. They need to meet or exceed the Canadian Food Inspection Agency standards.
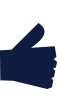
STEP 6
RESULTS AND APPROVAL
The laboratory results are reviewed by trained staff and the corresponding products become approved for use.
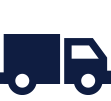
STEP 7
CUSTOMER DELIVERY
A final inspection of the product is done prior to loading it onto the truck for delivery to the customer.